What YOU Need to Know About Water Damage in Wood Floors
- Joe Huggins
- Jul 9, 2021
- 4 min read
Whether it was a malfunctioning dishwasher, an overflowing toilet, or a washing machine hose that split, water can get to your hardwood floor. Unfortunately, water and wood do not play well together. When wood floors are exposed to water, damage is inevitable. But there are some things you can do to minimize the damage. If you act quickly, you can prevent further damage. The first thing you need to do is to soak up or remove as much water as possible. If caught quickly enough, water damaged floors can simply be refinished to restore them to their original condition. At Luxury Wood NYC, we will always refinish your floors, if possible, rather than replacing them because restoration can save you thousands over total replacement.
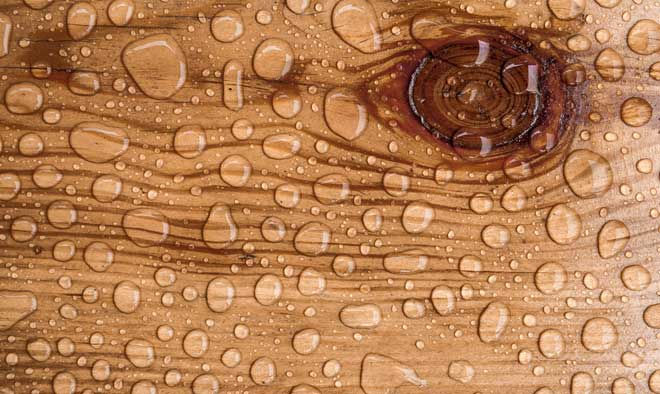
Signs of Hardwood Floor Water Damage to Look for:
Is the damage bad enough to call in hardwood floor experts, or will the floor recover on its own? It’s hard to tell sometimes. Depending on the type of hardwood floor you have, damage and repair will be different. Here are some signs to look for:
Cracking and Peeling – if it only affects the finish, this damage may be repairable by simply sanding and refinishing the surface.
Cupping – when the edges of each plank rise. Cupping means that the hardwood floor still has a lot of moisture in it.
Crowning – when the floor has dried completely, it will usually crown or rise in the middle of each plank. This gives it a rounded, pillowed appearance. Crowning will require sanding and refinishing to repair.
Buckling – buckling is the worst sign of water damage and usually occurs when the moisture has totally permeated the wood. If the leak is not immediately discovered and the water is allowed to sit on the wood for an extended period and seep in slowly, buckling will occur. Buckling is the wood plank itself warping and twisting. If your planks are twisted or bent upward, the floor will have to be removed and replaced.
The Experts at Luxury Wood NYC Will Minimize Wood Floor Repair Time and Costs
At Luxury Wood NYC, we are experts at hardwood floor water damage repair and restoration. Our goal is to repair what we can and replace what we must. We will do our best to minimize the replacement costs and time. Many times, we can replace only the damaged area and weave the new planks seamlessly into the existing wood floor. Then we can sand and refinish the entire floor, so everything matches perfectly. Whether we repair or replace your wood floor, it will look brand new when we’re done.
It is important to understand that water will migrate to areas below the wood floor system anytime there is a flood. When water damage occurs, the wood flooring and sub-flooring systems must be evaluated to determine the extent of damage and ensuing repairs.
Subfloor Materials Evaluation
Plywood: swelling, distortion, and delamination can occur when exposed to high moisture levels. Moisture tests should be conducted using insulated pin, hammer-probe type meters on the surface, backing, and core, and in several areas of the damaged material to accurately assess moisture.
Concrete: concrete is a porous material. It typically does not become damaged when exposed to water; however, adhesives, sealers and other compounds will slow the drying of a wetted concrete slab.
Drying: Dehumidifiers, heat, or regular airflow can accelerate the drying process. However, the subfloor should be within the flooring and adhesive manufacturer’s required moisture levels before flooring can be installed.
Wood Flooring Materials Evaluation & Remediation
Identify the type of flooring and installation methods.
Identify type of substrate.
Existing materials below the flooring surface may create additional mitigation costs and concerns (i.e., asbestos underlayment, radiant heating systems, etc.).
Determine the target moisture content for the geographic area and for the facility.
Reference the Equilibrium Moisture Content Chart (EMC) chart.
Consider the time of year repairs are to take place and assess the HVAC systems’ ability to sustain an adequate environment.
Conduct moisture testing.
Use insulated pin, hammer-probe type meters to achieve readings at multiple depths of flooring and sub-flooring material.
Use pin-less, dielectric meters to scan the flooring surface and map the damage.
Check existing, unaffected wood for reference.
Target should be within 2% of expected “in-use” moisture content.
Use dehumidification systems to stabilize the ambient conditions and bring them within the target range.
Some of the most effective types of dehumidification systems include desiccant systems and low-grain refrigerant systems.
Dehumidifiers should be placed on the flooring surface as well as below the flooring surface (when applicable).
Unconditioned areas directly below the wood sub-flooring system or sleepers, such as basements and crawlspaces, should also be opened to introduce heat and airflow. Any insulation on the underside of the floor joists should be removed.
Many times, damage will dissipate or even completely disappear as the flooring dries out over time.
Airflow and heat can be used to speed the natural drying process.
Vacuum extraction systems include placement of large mats/panels that are attached to vacuum/suction systems designed to pull water from the flooring surface.
Negative and positive air pressure systems force airflow beneath and within the flooring systems to decrease the moisture content by direct use of airflow.
A buckled wood floor requires replacement wherever the buckling has occurred. Once the flooring has buckled, the fasteners or adhesives are no longer effective, and the system will never return to its original state. Once the moisture source has been identified and eliminated, the buckled portion of the flooring may be replaced. The remainder of the flooring should be treated as noted.
If you suspect water damage, call Luxury Wood NYC at (908)-232-6600 and one of our hardwood water damage repair experts can help assess the situation and give you an estimate on repairing or replacing your water damaged wood floors.
Comments